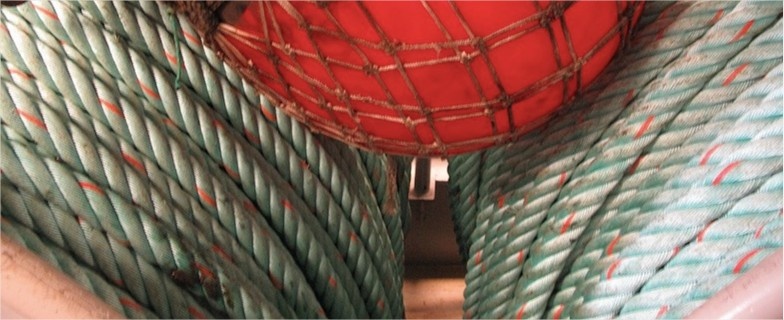
Seine Rope Technology Upgrade
With fishing doing well, fishing gear suppliers are having to boost their efforts to keep up with the need for fishing gear – and behind them are manufacturers like Euronete who have also had to ratchet up their productivity to meet the demand from their customers.
‘Our customers are doing well, which means that we are busier than ever,’ said Euronete’s Miguel Oliveira, while Jeroen Dorenbusch at IJmuiden Stores, the company’s Dutch outlet, said that ‘output for both wires and ropes are at unprecedented levels – which places some stresses on the supply chains.’
‘And that means investment.’ Miguel Oliveira added. ‘We are investing in production facilities and we have hired a lot of staff – which is some cases still hasn’t been enough.’
A part of parent company WireCo’s investment goes into research and development, and this has been streamlined to give Euronete a team of dedicated engineers working solely on fishing gears, both steel and synthetics.
‘I’m extremely happy with them and what they have achieved. Each one has a particular area of expertise and they are also closely involved with our dayto- day business,’ he said.
Euronete has been manufacturing and supplying flyshooting rope for more than ten years, and has invested in upgrading this product line
Of the range of innovations that the Euronete R&D team has been involved with, one of the real successes has been the EuroSeine® Premium rope that agents are already buying, even though it hasn’t yet come to the end of the long phase of at-sea testing.
‘This is a new flyshooting rope and with this being tested at sea in Scotland, Denmark and Norway, we are confident that we have something that will set a new standard in this market,’ Jeroen said.
‘We have been supplying EuroSeine for more than a decade now and we have a stable market for this with the Dutch fleet and parts of the French fleet, and it’s encouraging that the new vessels joining the fleet are choosing our seine rope.’
But with EuroSeine having only had a few minor tweaks and changes over the years, it was time for a look at this with fresh eyes, and what Euronete’s engineers have come up with is essentially a new product, designed from scratch, and with aspects of the manufacturing processes also redesigned to make new features and capabilities possible.
‘On sandy ground, we knew that our traditional rope works well,’ Miguel Oliveira said. ‘The challenges were in producing a rope that would cope even more effectively with rocky grounds, so this is a stiffer rope. As well as a new formulation of the steel and synthetic components of the rope, we have also looked at the construction and this was what required developing new machinery to make this possible.’
Jeroen commented that as a large manufacturer, Euronete has the entire process in house, able to begin with the raw materials to produce the fibres and then the strands, before these are used to form the finished four-stranded seine rope.
‘This has been a very difficult product to develop,’ Miguel Oliveira said. ‘We had worked on this before but we had to stop the development as it was becoming such an expensive process, so we can say that I have been looking for this product for the last twenty years, and I’m delighted that we have finally achieved this.’
‘We have also invested in the closing and stranding equipment,’ Jeroen Dorenbusch commented.
‘Traditionally seine netters have had coils of seine rope, and a lot of splicing. But now we are able to produce this in much longer lengths, depending on the weight and dimensions. We can produce 44m rope in lengths of 1500 to 1800 metres, and 50mm rope in 1350 to 1400 metres,’he said.
‘We’re a European manufacturer, with the whole production process in-house and with a fully integrated manufacturing chain, so we control the whole process from start to finish, and we can be certain of the quality at every stage.’


